What Do You Use a Flap Disc For?
Flap discs are an essential tool in the world of metalworking, woodworking, and various DIY projects. They consist of multiple overlapping layers, or flaps, of abrasive material that are attached to a central hub. The unique design allows for both grinding and finishing tasks, making flap discs versatile and widely used in several industries. This article will explore the various applications of flap discs, their advantages, and how to select the right flap disc for specific tasks.
Applications of Flap Discs
Flap discs are primarily used for grinding and finishing metal surfaces. They are commonly employed in tasks such as
1. Metal Fabrication In metal fabrication shops, flap discs are pivotal for preparing welds, blending seams, and smoothing rough edges on metal components. Their ability to remove material quickly while achieving a smooth finish makes them a favorite among metalworkers.
2. Woodworking In woodworking applications, flap discs are used to shape, grind, and finish wood surfaces. They help in contouring edges, removing paint or varnish, and polishing wood to achieve a beautiful, smooth finish.
3. Automotive Repair Mechanics often utilize flap discs for bodywork and paint removal. They are effective in smoothing out rough surfaces on vehicle frames and preparing them for painting.
4. Construction and Renovation In construction, flap discs assist in preparing surfaces for painting or coating. They can be used on concrete, steel, and other materials to achieve the desired texture and smoothness.
5. Restoration Projects For enthusiasts involved in restoration projects, flap discs provide an efficient means of stripping old paint or rust off various surfaces, allowing for a clean canvas for refinishing.
Advantages of Flap Discs
Flap discs present several advantages over traditional grinding wheels and sanding discs
what do you use a flap disc for
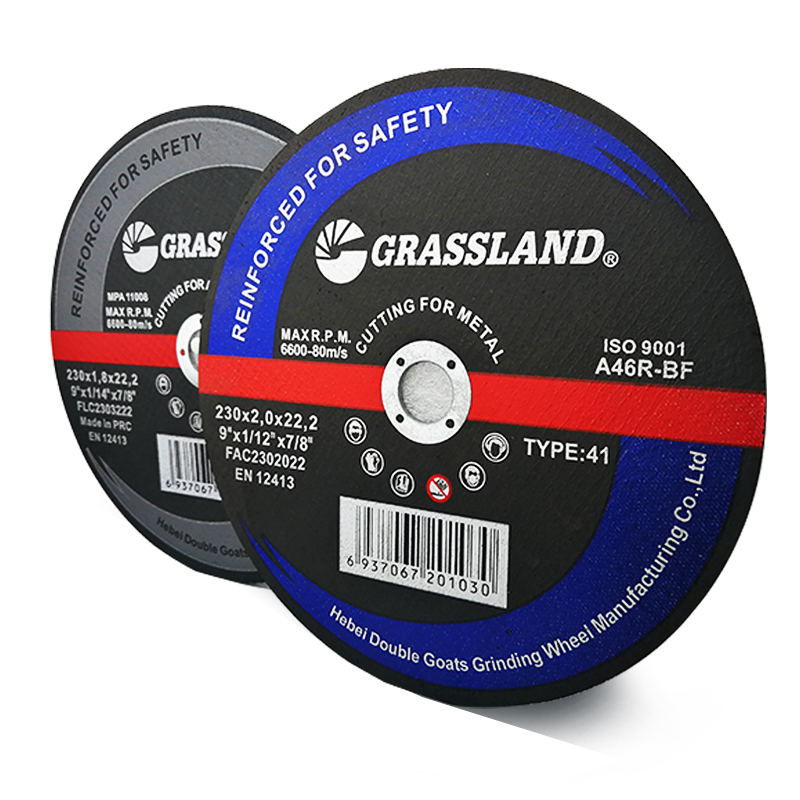
1. Versatility The dual functionality of flap discs allows users to grind and finish surfaces with a single tool, reducing the need for multiple abrasive products.
2. Efficient Material Removal Due to their design, flap discs offer excellent material removal rates, which speeds up the work process without compromising surface finish.
3. Less Heat Generation Flap discs tend to generate less heat compared to other grinding tools. This characteristic minimizes the risk of warping or damaging the workpiece, particularly with heat-sensitive materials.
4. Controlled Wear The layered structure of flap discs ensures consistent wear over time. As the flaps wear down, new abrasive material is exposed, maintaining effective cutting action and extending the disc's lifespan.
Selecting the Right Flap Disc
Choosing the right flap disc depends on several factors, including the material being worked on, the desired finish, and the specific task at hand. Here are key considerations
1. Material Type Different abrasive materials are suited for specific tasks. Aluminum oxide is common for general use, while zirconia is ideal for heavy grinding. Ceramic abrasives are excellent for stainless steel.
2. Grit Size Flap discs come in various grit sizes, ranging from coarse to fine. Coarse grits are effective for heavy material removal, while fine grits are suitable for finishing tasks.
3. Disc Shape Flat flap discs are ideal for flat surfaces, while contour flap discs are designed for irregular or curved surfaces.
In conclusion, flap discs are invaluable tools that offer efficiency and versatility for various grinding and finishing applications. Whether in metal fabrication, woodworking, automotive repair, or construction, flap discs provide precise material removal and a superior finish. By selecting the appropriate flap disc for your specific needs, you can achieve professional results in your projects.
Post time:Dec - 13 - 2024