Understanding Grinding Wheels An Essential Tool in Manufacturing
Grinding wheels are an indispensable tool in various manufacturing processes, serving as the backbone of material removal operations. Whether it's shaping metal, polishing surfaces, or sharpening blades, grinding wheels play a crucial role in the efficiency and quality of these tasks. In this article, we will delve into the construction, types, applications, and maintenance of grinding wheels to provide a comprehensive overview of their significance in industrial settings.
Construction of Grinding Wheels
A grinding wheel is essentially a wheel composed of abrasive particles bonded together with a matrix. The abrasives used can vary based on the type of material being worked on, the desired finish, and other operational parameters. The bonding agents—often made of resin, metal, or vitrified glass—hold the grains together while allowing for efficient chip removal during the grinding process. The structure of the wheel, which includes parameters like grain size, grade, and porosity, significantly influences its performance.
1. Abrasive Material Common materials include aluminum oxide, silicon carbide, and diamond. Aluminum oxide is versatile and used for general-purpose grinding, while silicon carbide is effective on harder materials. Diamond grinding wheels are ideal for cutting or grinding hard materials such as ceramics or glass. 2. Bonding Agents The bond determines a wheel's durability and performance in grinding operations. Resin-bonded wheels offer flexibility and are suitable for fine grinding, while vitrified bonds provide strength, making them ideal for heavy-duty applications.
3. Wheel Specifications Grinding wheels come in various sizes, shapes, and thicknesses, categorized by standardized systems. Typical specifications include the wheel’s diameter, thickness, and the type of arbor hole.
Types of Grinding Wheels
There are several types of grinding wheels, each tailored for specific applications
1. Flat Grinding Wheels These are the most common type, used for general purpose grinding tasks, such as surface grinding and tool sharpening.
2. Cylinder and Cup Wheels Designed for cylindrical grinding operations, these wheels shape and finish round surfaces effectively.
3. Tapered and Grinding Segments Tapered wheels and segments are often used for grindings that require precision, such as in sharpening tools or creating intricate designs.
Applications in Manufacturing
grinding wheels pdf
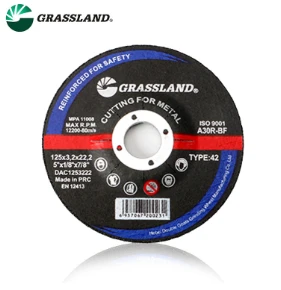
Grinding wheels find extensive use across multiple industries, including
- Metalworking They are critical in shaping, finishing, and tool sharpening, ensuring components meet precise specifications.
- Construction and Carpentry Used for cutting and grinding masonry materials and for finishing wood products.
- Automotive Integral to the production of components such as gears and axles, grinding wheels help in achieving tight tolerances and surface finishes.
- Aerospace In this sector, the need for precision and reliability makes grinding wheels vital for processing high-strength materials.
Maintenance and Safety
Proper maintenance of grinding wheels is essential to ensure their longevity and effectiveness. Key practices include
- Regular Inspection Check for signs of wear, damage, or imbalance. Any irregularities can pose serious safety risks.
- Proper Storage Store wheels in a dry, temperature-controlled environment to prevent moisture exposure that can compromise their integrity.
- Safe Operating Practices Always follow safety guidelines, including the use of personal protective equipment (PPE) and ensuring that the grinding machine is adequately guarded.
Conclusion
Grinding wheels are a vital component of the manufacturing process, enabling precision and efficiency across various industries. Understanding their construction, types, and applications is crucial for both operators and manufacturers looking to optimize their production capabilities. By adhering to proper maintenance and safety practices, users can maximize the lifespan and performance of grinding wheels, ensuring that they remain a reliable tool in the high-stakes environment of modern manufacturing.
Post time:Dec - 11 - 2024