Type 27 vs. Type 29 Flap Discs A Comprehensive Comparison
Flap discs are essential tools in the realm of grinding and finishing processes, primarily utilizing a robust backing plate with overlapping layers of abrasive flaps. Among the variety of flap discs available, Type 27 and Type 29 are two of the most commonly used designs, each tailored for specific applications and preferences. Understanding their characteristics, advantages, and appropriate uses can significantly impact project efficiency and outcome.
Design Differences
The primary distinction between Type 27 and Type 29 flap discs is their structural configuration. Type 27 flap discs feature a flat surface with the flaps oriented perpendicular to the back plate. This design excels in applications requiring a finished, smooth surface. The flat construction allows for even pressure distribution, making it ideal for working on flat surfaces or when performing finishing tasks.
On the other hand, Type 29 flap discs have a conical shape, with flaps angled upwards. This design provides greater aggression when grinding and is particularly advantageous for applications that involve contoured surfaces or when a significant amount of material needs to be removed quickly. The angle of the flaps allows for enhanced versatility, making it easier to address curved surfaces and edges.
Applications
When it comes to application, the differences between Type 27 and Type 29 flap discs become more pronounced. Type 27 discs are best suited for finishing work, such as rust removal, surface preparation for painting, and polishing tasks. Their design helps in achieving a finer finish, thereby reducing the amount of secondary work required after the initial grinding.
type 27 vs 29 flap disc
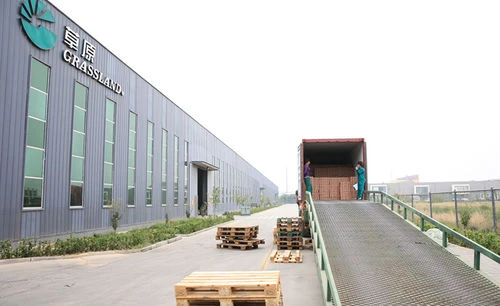
Conversely, Type 29 flap discs are frequently used for more aggressive grinding tasks. They are perfect for heavy stock removal, surface leveling, and deburring. Professionals often choose Type 29 discs when working on welds, sharp edges, or when precision is less critical than the speed of material removal. The adaptability of Type 29 discs makes them well-suited for a variety of materials, including metal, wood, and fiberglass.
Materials and Grit Selection
Both types of flap discs are available in various materials and grit sizes, providing flexibility based on the specific needs of a task. Aluminum oxide is among the most common abrasive material used for both types, known for its durability and effectiveness on steel and iron. Zirconia and ceramic flap discs are also available for more demanding applications, providing longer life and faster cutting rates.
Grit selection plays a crucial role in determining the performance of flap discs. Coarse grits (such as 36-60) are ideal for quick material removal, while finer grits (120-320) work well for finishing tasks. Understanding the material being worked on and the desired finish will help in choosing the right grit and type of flap disc.
Conclusion
In conclusion, choosing between Type 27 and Type 29 flap discs hinges on the specific requirements of a project. Type 27 discs are more suitable for finishing and polishing tasks on flat surfaces, while Type 29 discs excel in aggressive grinding applications on contoured or irregular surfaces. By taking into account the intended application, material, and desired finish, users can select the appropriate type of flap disc to achieve optimal results efficiently. Ultimately, both types have indispensable roles in metalworking and fabrication, offering unique advantages that cater to diverse industry needs.
Post time:Dec - 11 - 2024