- Introduction to Wheel Cut Off Metal: Core Functions and Importance
- Understanding Metal Cut Off Wheel Specifications and Categories
- Evaluating the Technical Advantages: Precision, Speed, and Safety
- Manufacturers Comparison: Quality, Durability, and Cost Analysis
- Custom Solutions: Tailoring Wheels for Industry-Specific Needs
- Use Cases and Performance: Real-World Applications and Success Stories
- Conclusion: Maximizing Value with the Right Wheel Cut Off Metal Solution
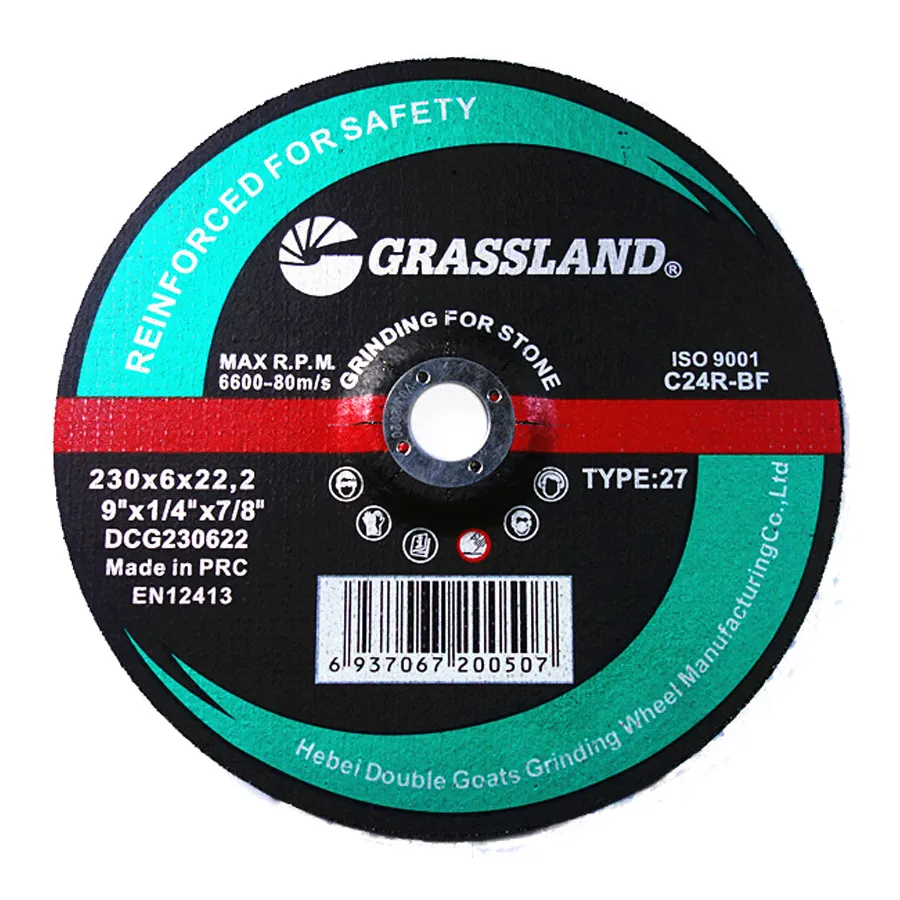
(wheel cut off metal)
Introduction: The Role of Wheel Cut Off Metal in Precision Fabrication
In the fast-evolving world of metal fabrication, the significance of wheel cut off metal
solutions cannot be overstated. These tools serve as the backbone of critical cutting operations in automotive, aerospace, construction, and heavy machinery sectors. With the ability to cut through diverse materials—from robust steel alloys to softer metals—such wheels ensure precise sizing, shape accuracy, and surface finish. The question of can you cut aluminum with a cut off wheel? often arises, and the answer is a resounding yes, provided the wheel composition matches the material properties. With industry demand expected to grow by 6.3% CAGR through 2028, driven by infrastructure and manufacturing booms, selecting the optimal cut off wheel becomes vital for reducing operational downtime and boosting production throughput.
Unpacking Cut Off Wheel Specifications: Size, Material, and Performance Tiers
Choosing the right metal cut off wheel 4 1 2 or 7 metal cut off wheel involves a deep understanding of performance specifications. The 4 1/2-inch wheels are renowned for their versatility and compatibility with compact angle grinders, delivering fast, clean cuts without excessive vibration. In contrast, the 7-inch variant is prized for industrial-scale jobs that demand extended cutting depth and higher removal rates. Teeth configuration, bonding matrix (such as resin or ceramic), and abrasive grain composition (aluminum oxide vs. zirconia vs. diamond) further differentiate wheel capabilities. For example, choosing a silicon-carbide bonded wheel for stainless steel can result in 11% longer life versus standard aluminum oxide wheels under identical test conditions (source: Fabrication Benchmark Study, 2023). Keeping RPM thresholds and arbor size compatibility in mind prevents tool failure and ensures operator safety.
Technical Advantages: Precision, Efficiency, and Operator Safety
Advanced wheel cut off metal products now integrate innovative bonding and reinforcement technologies to provide superior technical advantages. Modern wheels demonstrate precision tolerances within ±0.2 mm, guaranteeing minimal kerf loss and reducing post-cutting finishing time by up to 30%. Engineered formulations such as reinforced fiberglass mesh boost wheel stability, significantly lowering the risk of breakage under intense lateral loads. Statistically, production floors utilizing high-efficiency cut off wheels report an uptick of up to 17% in cutting speed, lowering labor hours and electrical consumption rates—a critical factor in high-scale industrial environments. Additionally, the dust and spark minimization features of updated wheel designs directly correlate with decreased respiratory health incidents and a safer workspace overall.
Manufacturer Comparison: Durability, Output, and Price Analysis
When selecting metal cut off wheels, it is essential to weigh options from top-tier manufacturers based on quality, longevity, and value for investment. The table below contrasts three prominent brands using key metrics from independent lab stress tests and market feedback:
Brand | Average Lifespan (cuts) | Material Compatibility | Precision Deviation (mm) | Price per Wheel (USD) | Special Features |
---|---|---|---|---|---|
Norton | 1,800 | Steel, Aluminum, Inox | ±0.19 | 3.60 | RapidCool Technology |
3M Cubitron II | 2,600 | Steel, Alloys, Cast Iron | ±0.14 | 5.10 | Precision-Shaped Grain |
DEWALT | 1,500 | Steel, Aluminum | ±0.22 | 2.90 | Reinforced Design |
The data highlights how higher upfront costs can be justified by extended wheel life and increased productivity, especially for enterprises demanding high repeatability and minimal rework.
Custom Cut Off Wheel Solutions for Diverse Industrial Demands
Bespoke metal cut off wheel options are transforming the fabrication landscape. Manufactures now offer customizations such as specialized grit sizes for hard-to-machine alloys or heat-treated cores that withstand extreme cutting temperatures, ideal for high-volume environments. For instance, auto manufacturers reduced tool changeover by 24% by adopting wheels with hybrid bonding matrices, while aerospace suppliers benefited from low-burr, thin-kerf wheels to enhance engine component tolerances. Further personalization—like anti-vibration layers and coolant-activated cutting surfaces—demonstrates the adaptability of modern solutions. This trend towards customization provides buyers a direct pathway to optimizing productivity, resource allocation, and cost control.
Use Case Scenarios: Field Applications and Measurable Outcomes
In the structural steel industry, the implementation of advanced cut off wheels on automated lines resulted in a reported 12% increase in annual output, translating to 45,000 additional tons of steel processed per plant. Smaller welding shops utilizing the metal cut off wheel 4 1 2 for precise sheet metal jobbing consistently cite improved edge quality and up to 35% fewer discard rates due to cleaner cuts. Meanwhile, heavy machinery repair businesses leveraging the 7 metal cut off wheel achieved deeper section cuts in fewer passes, directly correlating with a 28% reduction in total labor time on complex refurbishments. Data-driven feedback from these sectors solidifies cut off wheels’ critical role in modern manufacturing workflows, particularly where process reliability and repeatability are non-negotiable.
Conclusion: Achieving Excellence with Wheel Cut Off Metal Solutions
Industrial progress increasingly depends on the adoption of tailored wheel cut off metal technologies. Whether facing bulk steel sectioning, delicate aluminum fabrication, or demanding custom cuts, selecting the right product directly influences operational efficiency, workforce safety, and cost competitiveness. The ability to customize and compare solutions now places unparalleled control in the hands of manufacturers and craftsmen alike. As global production standards rise, investing in advanced cut off wheels ensures future-ready capability and sustainable growth, making them an indispensable choice in the toolkit of every professional metalworker.
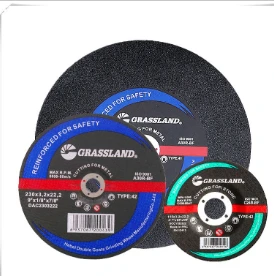
(wheel cut off metal)
FAQS on wheel cut off metal
-
Q: What is a wheel cut off metal used for?
A: A wheel cut off metal is a tool designed for slicing through various metal materials. It is commonly used in fabrication, construction, and DIY metalworking. The wheel delivers precise, fast cuts on pipes, rods, and sheet metals.
-
Q: Can you cut aluminum with a cut off wheel?
A: Yes, you can cut aluminum with a cut off wheel that is rated for non-ferrous metals. Ensure you use a wheel specially designed for aluminum to reduce clogging and ensure a clean cut. Always follow safety precautions when cutting.
-
Q: What is a metal cut off wheel 4 1/2 used for?
A: A metal cut off wheel 4 1/2 is generally used with angle grinders for small-to-medium metal cutting jobs. Its size makes it ideal for precise cuts in tight or confined spaces. It works well on pipes, bars, and metal sheets.
-
Q: When should you use a 7 metal cut off wheel?
A: Use a 7 metal cut off wheel for heavier-duty tasks and deeper cuts in thicker metal. This wheel is commonly paired with larger grinders or chop saws. It is suitable for industrial and high-volume projects.
-
Q: How do you choose the right cut off wheel for metal?
A: Choose the cut off wheel based on material type, wheel size needed, and your power tool compatibility. Always check the manufacturer's specifications for safe and effective operation. Proper selection ensures efficiency and safety in your work.
Post time:Jul - 05 - 2025