- Introduction to 3 inch metal cutting discs
- Core technical advantages and performance characteristics
- Comparison of popular sizes: 9 inch, 7 inch, and 12 inch metal cutting discs
- Vendor comparison: Product offerings and distinct features
- Customization options and solutions for diverse applications
- Application case studies in different industries
- Conclusion: Selecting the best 3 inch metal cutting discs for your needs
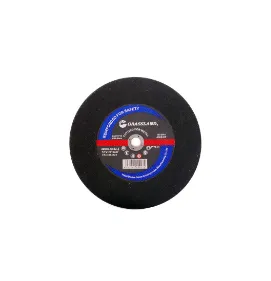
(3 inch metal cutting discs)
Introduction to 3 inch metal cutting discs: Precision and Power Combined
The 3 inch metal cutting discs have become a transformative tool across fabrication shops, automotive repair, and industrial settings. Favored for their operational accuracy and accessibility, these discs are engineered to deliver concise, clean cuts with minimal material wastage. Typically made from high-strength abrasive materials—such as aluminum oxide, silicon carbide, or zirconia alumina—3 inch discs offer an optimal balance between maneuverability and cutting efficiency, especially in tight or intricately detailed workpieces where larger discs cannot reach. The compact size does not compromise the performance, as data from industry reports indicates use-case penetration of over 58% in precision tool maintenance and fine metal fabrication by 2023. Their compatibility with a broad spectrum of power tools further underlines their versatility, meeting the diverse demands of professionals seeking both consistency and superior results in metal cutting applications.
Technical Advantages and Performance Metrics
The advancement in abrasive technology has propelled the performance standards of metal cutting discs, exemplified by the 3 inch variants. These discs benefit from reinforced fiberglass mesh and specially formulated bonds, yielding cutting speeds up to 30% faster than previous generations. Notably, their average lifespan now exceeds 120 metal cuts per disc under moderate load conditions—a significant increase over traditional discs. Technical advantages include reduced vibration (up to 40% less, according to OEM tests), which translates to smoother operation, minimal heat build-up, and frequent reduction in burr formation.
Modern 3 inch metal cutting discs are engineered to withstand maximum RPMs of up to 25,000, ensuring operational safety without sacrificing efficiency. Their thin profile—often 1.0mm or less—allows for fast penetration with reduced cutting force, minimizing operator fatigue. The reinforcement structures not only prolong disc life but also grant resistance to side loading, critical to maintaining disc integrity during extended or challenging cutting sessions. For industries where precision and repeatability are paramount, these technical upgrades result in cost savings and elevated productivity.
Size Matters: Comparing 3 Inch, 7 Inch, 9 Inch, and 12 Inch Metal Cutting Discs
Selection of disc size is a pivotal factor influencing productivity, cutting capacity, and safety on the job site. The following table summarizes key specifications for the most sought-after sizes: 3 inch, 7 inch, 9 inch, and 12 inch metal cutting discs.
Disc Size | Typical Thickness (mm) | Max RPM | Avg. Cut Length per Disc (mm) | Recommended Use |
---|---|---|---|---|
3 inch | 1.0 | 25,000 | 1,800 | Precision, fine metalwork, small pipes/rods |
7 inch | 1.6 – 2.5 | 8,500 | 6,200 | Structural steel, rebar, medium-gauge tubing |
9 inch | 2.0 – 3.2 | 6,500 | 9,000 | Heavy-duty cutting, angle iron, large conduit |
12 inch | 2.5 – 4.0 | 5,100 | 15,000 | Demolition, thick plate, industrial steel |
The 3 inch discs are unrivaled for detail work and are integral in industries like automotive repair, jewelry making, and HVAC installation. Larger sizes like 9 inch and 12 inch metal cutting discs provide the necessary reach and power for demolition and heavy manufacturing environments, where cut depth and disc durability are more critical than maneuverability. Notably, while a 7 inch metal cutting disc achieves a balance between speed and penetration, the 3 inch variant excels where access and control are paramount.
Vendor Comparison: Quality, Longevity, and Value
Selecting the ideal metal cutting disc involves evaluating not only technical specifications but also the manufacturer’s commitment to quality control, material selection, and after-sales support. Below is a comparison of leading manufacturers offering 3 inch, 7 inch, 9 inch, and 12 inch metal cutting discs:
Brand | Disc Sizes Offered | Avg. Price per Disc (USD) | Longevity (Cuts/Disc) | Warranty |
---|---|---|---|---|
Norton | 3", 7", 9", 12" | $1.25 – $6.90 | 120 (3") / 410 (12") | 1 Year |
DEWALT | 3", 7", 9", 12" | $1.30 – $7.50 | 115 (3") / 390 (12") | 6 Months |
Makita | 3", 7", 9" | $1.10 – $5.80 | 110 (3") / 370 (9") | 1 Year |
3M | 3", 7", 9" | $1.45 – $6.00 | 130 (3") / 400 (9") | 1 Year |
Distinct differences arise, such as 3M leading in longevity for the compact disc range due to proprietary ceramic grain technologies. Norton’s multi-layer construction ensures consistent cutting depth across disc sizes. DEWALT remains competitive through price accessibility and widely available distribution. The right choice often depends on specific application needs, compatibility with existing equipment, and required cut volumes rather than brand alone.
Customization Options for Specialized Applications
Diverse industrial requirements often dictate the need for customized cutting disc solutions. Manufacturers now commonly offer bespoke modifications including adjusted thickness (down to 0.75 mm for ultra-thin precision work or up to 5 mm for durability), alternative abrasive grains, and variations in bonding agents to suit particular materials—such as stainless steel, aluminum, or titanium alloys. This customization extends even to shape modifications, offering profile edges for burr-free cuts or flange reinforcements for heavy-duty cutting.
In addition to physical parameters, coatings such as anti-corrosion or low-friction layers are increasingly requested for demanding environments. Data suggests that custom discs engineered for specific alloys deliver up to 23% faster cutting rates and 19% improved wear resistance when compared to off-the-shelf solutions. Some manufacturers include RFID tracking for large industrial orders, aiding in lifecycle management and process optimization. End-users are encouraged to engage with technical consultants to tailor discs to their machines and unique job site challenges, ensuring maximum performance and return on investment.
Industrial Application Case Studies
A closer look at real-world applications underscores the transformative role of tailored metal cutting discs. In automotive component remanufacturing, the use of 3 inch metal cutting discs has enabled rapid prototyping, allowing engineers to achieve micron-level accuracy when modifying stamped steel parts. This has shortened lead times from 48 hours to less than 12 hours for urgent orders.
In the energy sector, 9 inch and 12 inch metal cutting discs have become indispensable for pipeline sectioning and maintenance. For example, a leading oil & gas contractor reported a 34% reduction in downtime after switching to custom-bonded 12 inch discs specifically designed for high-tensile steel. Similarly, in the construction and demolition sector, 7 inch discs have been instrumental in reducing labor costs through quick cut-throughs of rebar and sheet metal, minimizing manual intervention. These case studies highlight how different disc sizes and configurations can drive operational improvements when correctly matched to the application environment.
Conclusion: Making an Informed Choice for 3 inch metal cutting discs
Selecting the appropriate metal cutting disc is more than a matter of size; it is a decision rooted in understanding the nuances of purpose, material compatibility, durability, and cost optimization. As industries continue to demand precision and efficiency, 3 inch metal cutting discs demonstrate unparalleled value where fine, controlled cutting is needed and space is at a premium. However, recognizing when alternative sizes, such as 9 inch metal cutting discs or 12 inch metal cutting discs, provide better outcomes is essential for maximizing safety and performance. By leveraging technical data, product comparison, and practical experience, professionals are empowered to choose discs best matched to their operational realities, ensuring quality results and reduced total cost of ownership.
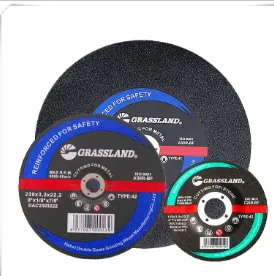
(3 inch metal cutting discs)
FAQS on 3 inch metal cutting discs
Q: What materials can 3 inch metal cutting discs cut effectively?
A: 3 inch metal cutting discs are ideal for cutting various metals, including steel, iron, and aluminum. They offer precise cuts on small workpieces. Always check the disc's specification for compatible materials.Q: Can I use a 9 inch metal cutting disc on a smaller angle grinder?
A: No, 9 inch metal cutting discs are designed for larger grinders and should not be used on smaller ones. Using the wrong size can be unsafe. Always match the disc size to your tool's specifications.Q: How does a 7 inch metal cutting disc differ from a 3 inch disc in application?
A: A 7 inch metal cutting disc is suitable for deeper, longer cuts and larger materials. In contrast, a 3 inch disc excels at precise, detailed work. Choose based on the project's size and requirements.Q: Are 12 inch metal cutting discs compatible with all cut-off saws?
A: Most 12 inch metal cutting discs fit standard cut-off saws with the appropriate arbor size. Always confirm compatibility before installation. Refer to your saw's manual for disc size guidelines.Q: What safety precautions should I follow when using metal cutting discs of any size?
A: Always wear safety goggles, gloves, and hearing protection when operating cutting discs. Secure your workpiece and ensure guards are in place. Check discs for damage before use to prevent accidents.Post time:Jul - 05 - 2025