Understanding the Difference Between Cutting Discs and Grinding Discs
When it comes to metalworking, construction, or any DIY project involving materials like metal or concrete, the tools you choose can significantly affect the quality of your work. Among these tools, cutting discs and grinding discs play crucial roles, yet they serve different purposes. Understanding the differences between these two types of discs can help you select the right tool for your specific needs, leading to better results and greater efficiency.
Cutting Discs
Cutting discs, often referred to as cut-off wheels, are designed specifically for slicing through various materials. These discs are typically thinner than grinding discs, ranging from 0.045 inches to about 0.125 inches in thickness. This design allows them to make clean, precise cuts without excessive material removal. Cutting discs are available for various materials, including metal, masonry, and plastic, and are often made from abrasive materials like aluminum oxide or diamond particles.
When using a cutting disc, it's essential to operate the tool at the correct speed, adhering to the manufacturer's recommendations. A proper technique involves applying light pressure and letting the disc do the work, as applying too much force can cause overheating or even breakage of the disc. Cutting discs are commonly used in applications such as pipe cutting, metal sheet cutting, and other situations where a straight, clean cut is necessary.
Grinding Discs
On the other hand, grinding discs are thicker and designed for grinding, shaping, and finishing materials rather than cutting them. Typically available in thicknesses ranging from 0.25 inches to more than half an inch, grinding discs offer greater durability and stability for tasks that require removing material or smoothing surfaces. They are used to eliminate burrs, polish surfaces, or prepare materials for welding.
Grinding discs come in a range of grit sizes, allowing users to select the appropriate disc based on the desired finish and material removal rate. Coarse grits are used for heavy material removal, while finer grits are employed for polishing or finishing work. Similar to cutting discs, grinding discs can be made from materials like aluminum oxide, silicon carbide, or diamond, depending on the application's requirements.
Key Differences
diferencia entre disco de corte y desbaste
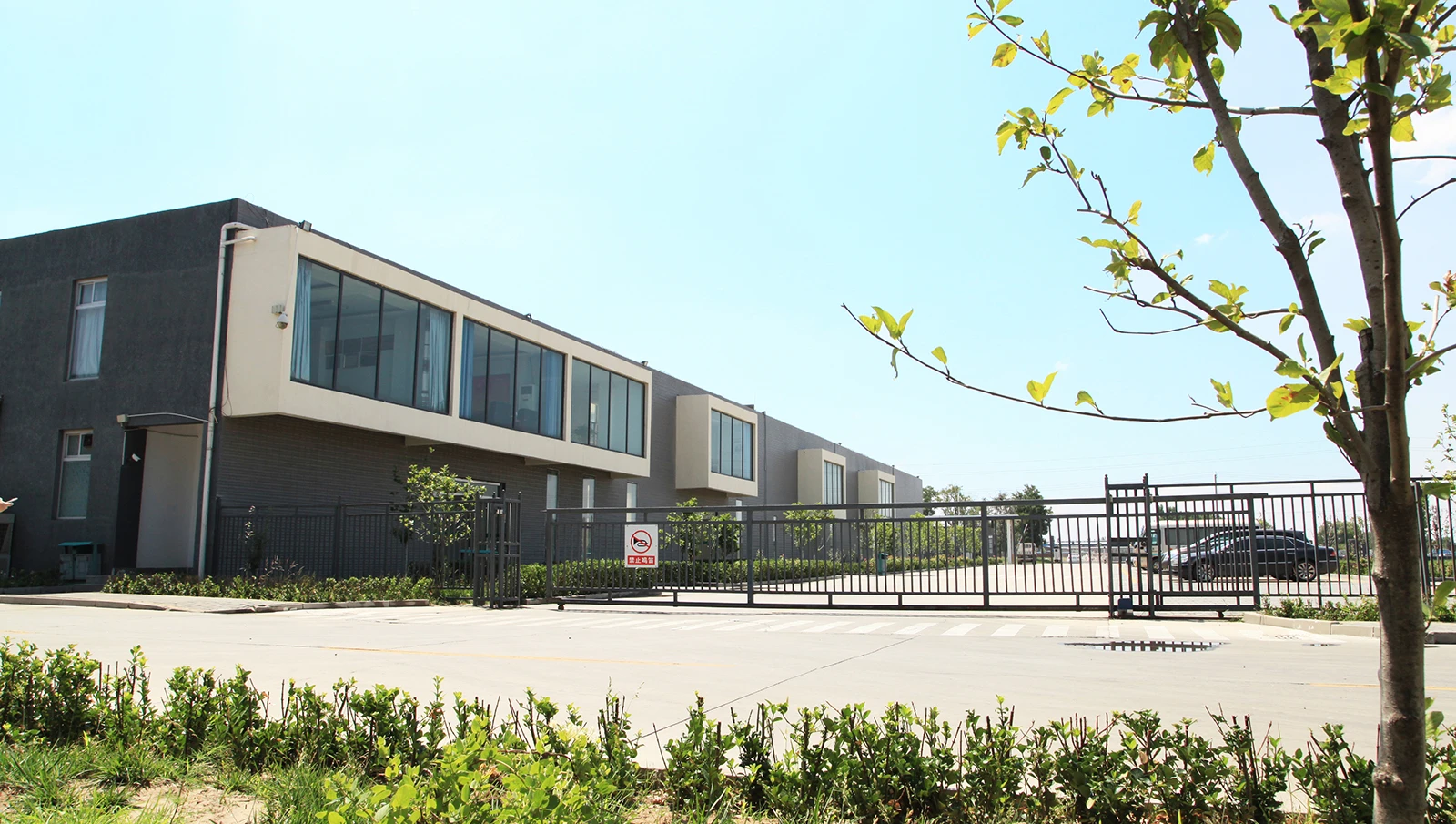
While cutting and grinding discs may appear similar, several fundamental differences distinguish their functions and designs
2. Thickness Cutting discs are generally thinner than grinding discs, allowing for cleaner cuts with less material removal.
3. Material Removal A cutting disc focuses on making clean cuts and removes minimal material, whereas a grinding disc actively removes material to shape and finish surfaces.
4. Grit Options Grinding discs offer a variety of grit sizes, catering to different levels of material removal and surface finishing, whereas cutting discs typically do not come in various grits.
5. Application Techniques When using cutting discs, users should apply minimal pressure and allow the disc to make the cut; in contrast, when grinding, more pressure can be applied to allow for effective material removal.
Conclusion
In conclusion, understanding the difference between cutting discs and grinding discs is essential for anyone involved in metalworking or construction. Utilizing the correct disc for your specific task will not only improve the quality of your work but also enhance your efficiency and safety. Remember to closely follow the manufacturer’s guidelines for speed and pressure to maximize the lifespan of your tools and achieve the best results possible. Choosing wisely between cutting and grinding discs can lead to impressive craftsmanship and a streamlined workflow in any project you undertake.
Post time:Nov - 26 - 2024