The Importance of Choosing the Right Cutting Wheel for Cast Iron
When it comes to metalworking, particularly in fabrication and machining processes, the choice of cutting tools is crucial for achieving optimal results. Among the various materials used in manufacturing, cast iron is one of the most common due to its excellent casting properties and versatility. However, cutting cast iron requires specific tools designed to handle its unique characteristics. This is where cutting wheels come into play, specifically designed for cast iron applications.
Understanding Cast Iron
Cast iron is an alloy of iron, carbon, and silicon, known for its excellent wear resistance and ability to withstand high temperatures. It is often used in industries such as automotive, construction, and machine manufacturing. While cast iron is relatively easy to cast, it can be challenging to cut due to its brittleness and tendency to produce sharp, jagged edges. Therefore, using an appropriate cutting wheel is vital for achieving clean, precise cuts while minimizing the risk of tool wear and breakage.
Choosing the Right Cutting Wheel
When selecting a cutting wheel for cast iron, there are several factors to consider
1. Material Composition Cutting wheels are made from various materials, such as aluminum oxide, zirconia, or diamond. For cast iron, aluminum oxide wheels are often recommended due to their durability and cost-effectiveness. Zirconia wheels can also be used for better performance, especially in heavy-duty applications.
2. Wheel Thickness The thickness of the cutting wheel can greatly influence its performance. Thinner wheels (typically 1/16 inch) provide faster cuts and less material removal, making them ideal for precise cutting tasks. However, they may wear out more quickly. Thicker wheels (1/8 inch or more) are more durable and suitable for heavy-duty applications, but they may slow down the cutting process.
3. Grit Size The grit size of the cutting wheel affects the finish of the cut. A finer grit (such as 36 or 40) will create a smoother finish but may cut slower. Conversely, a coarser grit (such as 24) will remove material faster but may leave a rougher edge. For cutting cast iron, a medium grit size is typically ideal, striking a balance between speed and finish quality.
cutting wheel for cast iron
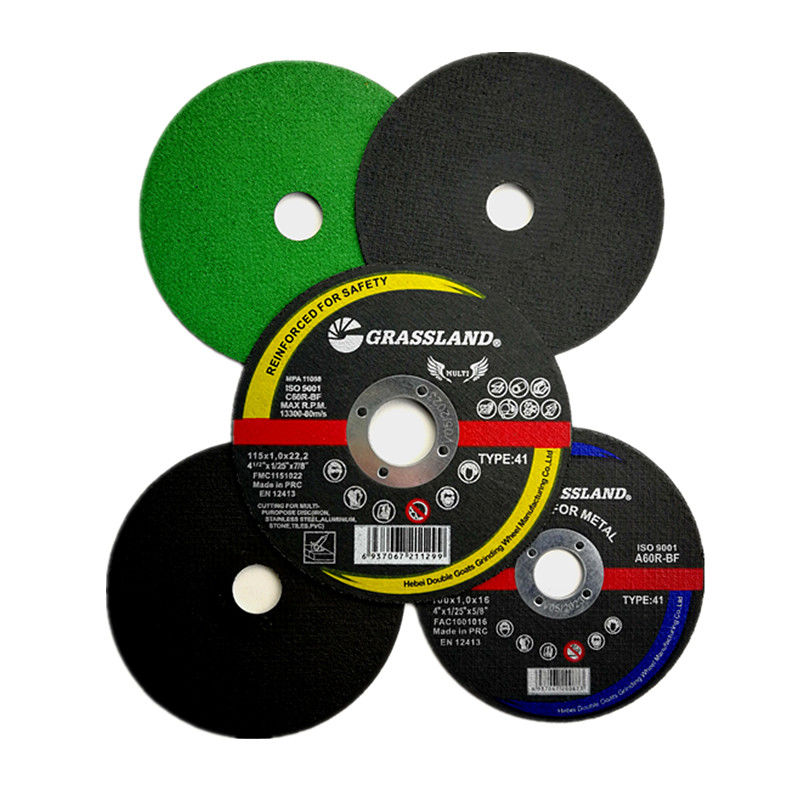
4. Speed Ratings Always check the maximum RPM rating of the cutting wheel to ensure compatibility with the cutting tool. Cast iron often requires higher speeds for efficient cutting, and using a wheel with a lower RPM rating could lead to accidents or poor cutting performance.
5. Cooling and Lubrication Cast iron can produce significant heat during cutting, which can lead to premature wear of the cutting wheel. Using a cutting fluid or lubricant can help dissipate heat, prolonging the life of the wheel and improving the quality of the cut.
Best Practices for Cutting Cast Iron
To maximize the effectiveness of your cutting wheel, it’s essential to follow best practices during the cutting process
- Secure the Workpiece Ensure that the cast iron piece is firmly secured to prevent vibrations that can compromise the cutting accuracy and damage the wheel. - Consistent Feed Rate Maintain a steady feed rate while cutting; excessive force can lead to wheel breakage, while insufficient force can result in a poor cut.
- Regular Maintenance Inspect cutting wheels regularly for signs of wear and replace them as needed. A worn wheel not only offers poor cutting performance but also poses safety risks.
Conclusion
Cutting cast iron can be a straightforward task if you choose the right cutting wheel and follow proper techniques. By understanding the unique traits of cast iron and the specifications of cutting wheels, you can achieve precise cuts with minimal effort and wear. Whether you are a professional machinist or an enthusiast working on DIY projects, investing in a quality cutting wheel designed for cast iron will make a significant difference in your metalworking endeavors. Always prioritize safety and efficiency, and select tools that will enhance your production capabilities.
Post time:Oct - 02 - 2024